Oxyfuel создает химическую реакцию между кислородом и сталью, которая настолько горяча (около 1800 ° F), что металл размягчается, а затем плавится.
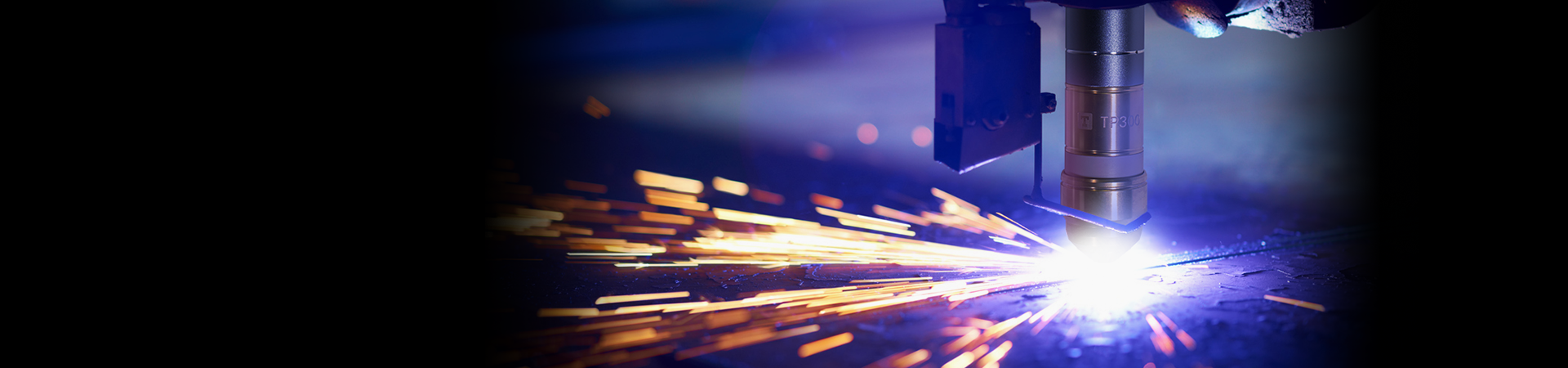
- БАЗОВЫЕ ЗНАНИЯ
- ХАРАКТЕРНАЯ ЧЕРТА
- СРАВНЕНИЕ
- КАЧЕСТВО РЕЗКИ
- ПРОИЗВОДИТЕЛЬНОСТЬ
- ЭКСПЛУАТАЦИОННЫЕ РАСХОДЫ
- Контакт
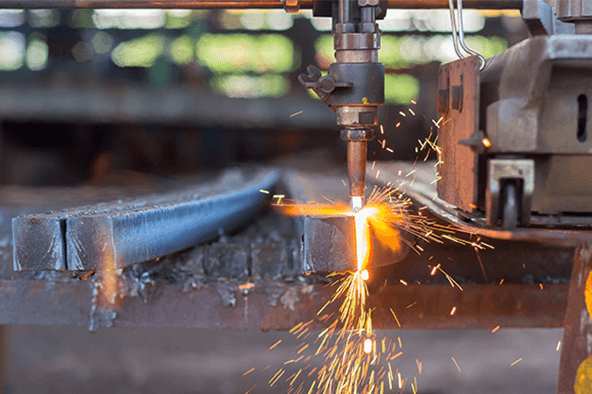
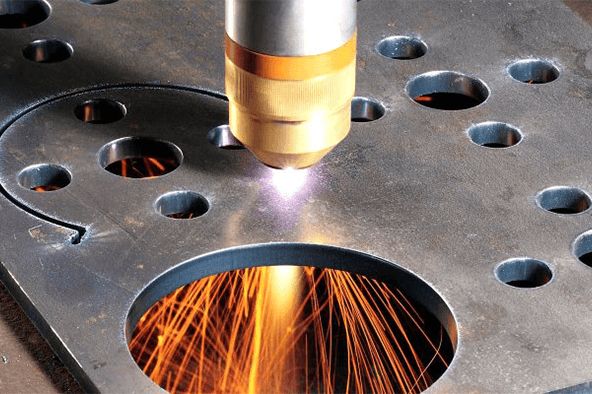
Плазма использует высокотемпературный ионизированный газ для создания очень горячей дуги с высокой плотностью энергии, которая может разрезать любой проводящий материал.
Oxyfuel создает химическую реакцию между кислородом и сталью, которая настолько горяча (около 1800 ° F), что металл размягчается, а затем плавится.
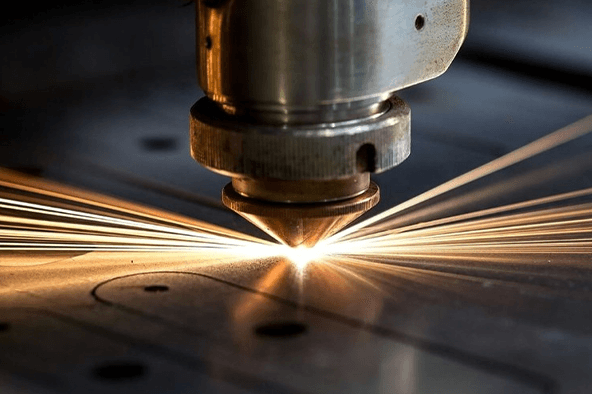
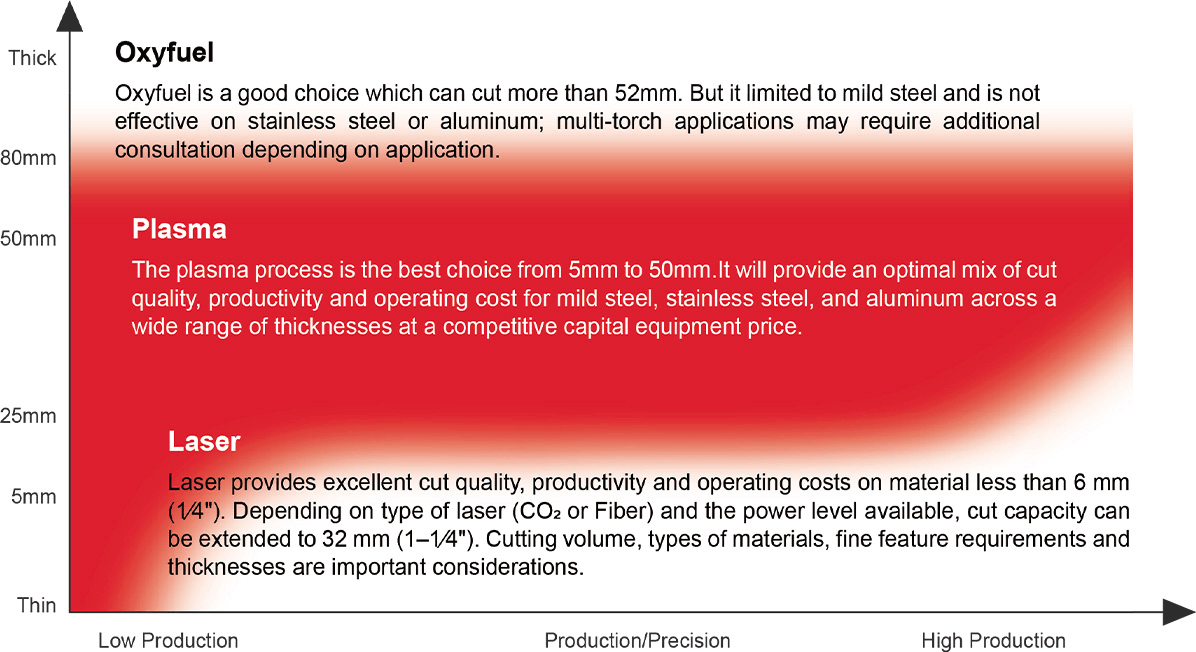
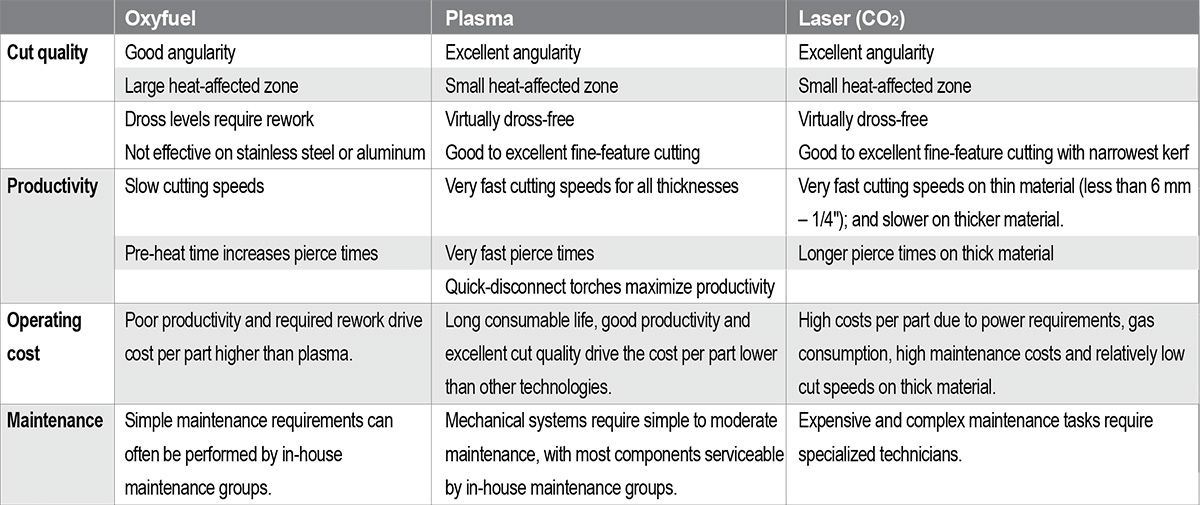
Разные виды резки требуют разного уровня качества резки. Это может быть важно, потому что обрезанный край будет виден покупателю готовой детали или продукта. В других случаях качество резки имеет значение из-за его влияния на последующие процессы, такие как сварка или покраска; готовые к сварке разрезы сократят потребность в подготовке к сварке, упростят производство и снизят трудозатраты. Бывают также случаи, когда качество резки не имеет большого значения, и операторы могут предпочесть качество резки в обмен на более высокую производительность.
Качество резки определяется рядом факторов, в том числе:
· Движение режущего станка
· Соответствует ли уровень мощности станка толщине разрезаемого материала
· Какие газы (или, в случае гидроабразивной резки, абразивы) используются
· Правильно ли подобраны настройки станка и расходные материалы для резки
В некоторых процессах, особенно при газокислородной резке, навыки оператора могут быть наиболее важным фактором, определяющим качество резки. Другие процессы не так сильно зависят от навыков оператора.
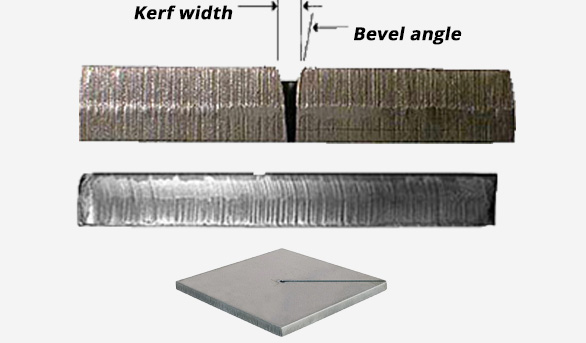
Качество огранки оценивают по следующим признакам:
· Угловатость – резка практически без угла считается лучшей
· Разрез или ширина – меньшая ширина разреза позволяет получить более мелкие детали
· Допуск – более жесткие допуски означают более точный и воспроизводимый рез.
· Размер зоны термического влияния - меньшая зона лучше защищает целостность металла и влияет на жизнеспособность других процессов, таких как сварка и нарезание резьбы
· Окалина – как правило, чем меньше, тем лучше (окалина – это металл, который плавится в процессе резки и остается прикрепленным к краям разреза)
· Качество кромки − гладкость отделки
· Эффективность контроля высоты резака (THC)
Производительность часто ошибочно отождествляют только со скоростью резки. Хотя важно, есть и другие факторы, которые следует учитывать. Например:
· Требуемое время программирования
· Время, необходимое для настройки работы на раскройном станке
· Время, необходимое для подготовки (или предварительного нагрева) системы к резке
· Количество режущих головок, которое может принять станок
· Эффективность программного обеспечения для раскроя и его способность максимизировать время резки и уменьшить ненужные движения режущей головки.
· Возможность безопасной выгрузки деталей во время резки
· Возможность выполнять несколько процессов на одном станке, например, резка контуров, резка внутренних пазов и отверстий, снятие фаски
· Интеграция систем для выполнения параллельных задач, таких как предварительная подача во время хода или IHS, может сократить время процесса.
· Время, необходимое для второстепенных операций, таких как шлифование, которое может быть уменьшено или устранено за счет улучшения качества деталей, сходящих с режущего станка.
На общую стоимость эксплуатации системы резки могут влиять многие факторы: расходные материалы, электроэнергия, газ, техническое обслуживание и т. д.
Стоимость рабочей силы
Стоимость рабочей силы также является важным фактором эксплуатационных расходов в большинстве частей мира; рост ставок труда и нехватка квалифицированной рабочей силы продолжают стимулировать спрос на автоматизированные решения для резки. Чтобы еще больше сократить эксплуатационные расходы, рассмотрите полностью автоматизированное решение, которое может уменьшить или устранить:
· необходимость программирования и настройки на ЧПУ
· вторичные операции, такие как шлифовка для подготовки к сварке
· потребность в более чем одной машине для выполнения нескольких технологических операций, таких как резка, маркировка и снятие фаски
Использование материала
Использование материалов является еще одним важным фактором, влияющим на эксплуатационные расходы. Хотя во многих случаях можно возместить некоторые затраты за счет продажи неиспользованного или бракованного материала, гораздо выгоднее увеличить использование этого материала, чтобы в первую очередь было меньше отходов. Разнообразие факторов способствует использованию материала; прежде всего, программное обеспечение САПР, которое определяет расположение деталей и управляет движением резки.
При расчете эксплуатационных расходов важно не подсчитывать только затраты в час, а вместо этого сосредоточиться на стоимости одной детали или стоимости фута. Почему? Система, которая стоит примерно 17,96 евро (20 долларов США) в час, но производит только две детали в час, не так эффективна, как система, которая стоит примерно 17,96 евро (20 долларов США) в час, но производит 100 деталей.
Стоимость одной детали = Эксплуатационные расходы в час / количество произведенных деталей
Стоимость за фут = Эксплуатационные расходы в час / количество срезанных футов
Общая стоимость
Еще более глубокая оценка эксплуатационных расходов требует понимания общих затрат на производство готовой детали, включая последующие процессы подготовки детали к сварке или окраске, или просто отделку детали в эстетических целях. Когда последующие процессы, а также затраты машинного времени и трудозатрат, которые они требуют, могут быть сокращены за счет усовершенствования процесса резки, общая стоимость готовой детали может быть снижена.
Одной из областей, которую часто упускают из виду в системе резки, является управление высотой резака (THC). Высокопроизводительный регулятор высоты имеет возможность автоматической настройки процесса с помощью ЧПУ или программы обработки деталей, чтобы:
· уменьшить или устранить распространенные ошибки настройки
· компенсировать износ электрода, чтобы максимально увеличить срок службы расходных материалов
· поддерживать правильную высоту для оптимальной угловатости резки
· обнаружение столкновений резака, защита резака от повреждений